-
Metal.Cutting.
Drilling / Sinking
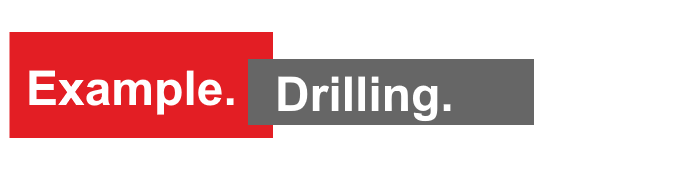

Drilling and milling with Lubrimat.

Drilling aluminium with Spraymat.

Drilling in St52 with Lubrimat.

Drilling, reaming and countersinking with Lubrimat.

Drilling Ø 4 and 16 mm in aluminium profiles with 4 x Pulsomat.

Drilling Ø 1 mm in brass tubes. Lubrimat improved tool life time and surface quality.
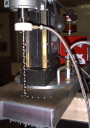
Drilling Ø 11.5 of a hole notch for a plasma cutting machine in X2CrNiMo22, 80 mm thick. Using internal MQL cooling and a Lubrimat resulted in a 20 fold increase in the edge life and savings on processing time of over 70%.

Drilling Ø 4 mm of aluminium rollers (Ø 250 mm) on a machine centre with Lubrimat.
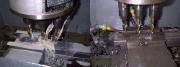
Drilling of rectangular steel tubes with Lubrimat. With MQL improved workplace safety. In addition, the lifespan of the drills trebled.
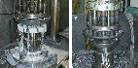
Drilling and countersinking of steel truck rims (Ø 36 / 26 mm). with a 10 spindle head. Lubrimat. Improving tool life by 30%.
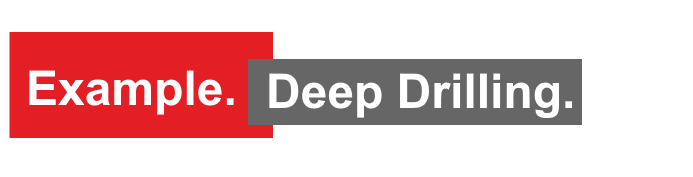

Deep hole drilling up to 800 mm with Toolmat.

Deep hole drilling (l/d ratio = 30) of hydraulic shafts using single-lip drills with Toolmat. When MQL is used, the lifespan of the drills exceeds the manufacturer's specifications by approx. 50%. The MQL spray air also has the useful function of blowing any chips out of the drill hole.

Deep hole drilling with Toolmat.

Deep hole drilling with Toolmat. Depth is over 80 times the diameter, aluminium pump cases at a drilling depth of 260 mm. Switching to MQL internal lubrication trebled the edge life in comparison to internal cooling using emulsion.

Deep hole drilling with Toolmat.
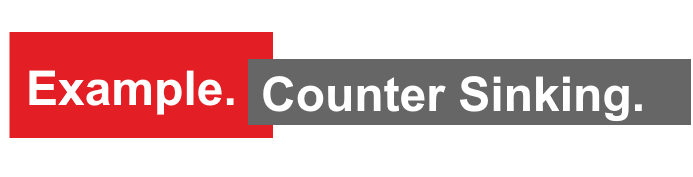

Countersinking of sheet steel 8 mm thick using Ø 20 mm carbide countersinks, hardened subsequently. Emulsion residues in the hardening furnace resulted in poor flue gas values and sooting of the furnace. With Lubrimat®, the countersink is lubricated using one nozzle, resulting in an edge life of 10,000 drill holes.

Countersinking (90°) of door furniture constructed of St37 (cold rolled) with coated HSS (high-performance speed cutting steel) countersinks. With Lubrimat® the lifespan of the machinery rose to 40,000 countersinks compared to 10,000 for dry processing.
Sawing
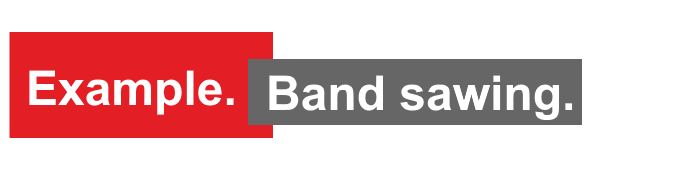
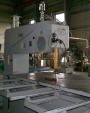
Sawing of copper plates with Lubrimat®

Sawing tubes up to Ø250 mm with Sawfix®

Sawing aluminium tubes , Ø400 mm with Lubrimat

Band sawing of aluminium tubing with Lubrimat®

Sawing steel tubes , Ø300 mm with Lubrimat

Sawing steel with Lubrimat
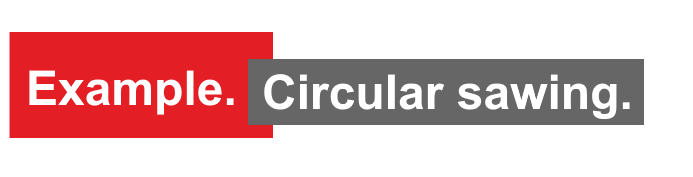
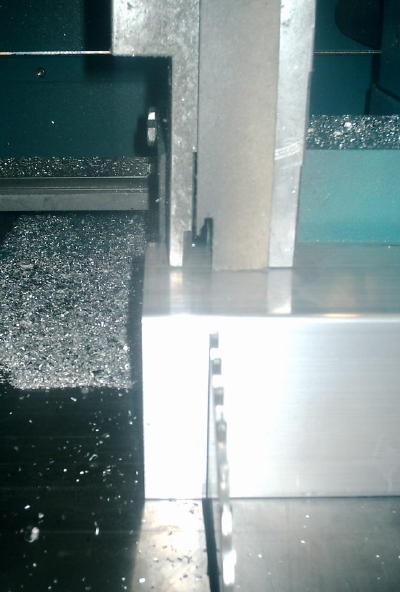
Sawing aluminium on a Kaltenbach SKL450NA, blade Ø600 mm, with Sawfix®

Cold circular sawing of steel rolls Ø400 mm with Lubrimat®. Because the saw was rarely used, the costs of maintaining and removing the emulsion bore far outweighed the saw's productivity. Switching to MQL means that emulsion is no longer required.

Circular sawing, span style=``font-variant: small-caps``> Kaltenbach sawing machine, sawing blade Ø 400 mm, with Sawfix®

Circular sawing of double-T-steel bars (1000 mm x 400 mm), blade Ø1200 mm, with Lubrimat®

Circular sawing, EISELE sawing machine, sawing blade Ø350 mm, with Sawfix®

Circular sawing of aluminum profiles with an ADIGE sawing machine, sawing blade Ø 315 mm, with Lubrimat®

Circular sawing with a TRENNJÄGER sawing machine, sawing blade Ø910 mm, with Lubrimat® with nozzle block increased tool life to 160%

Custom made sawing machine with 2 x Ø250 mm blades with Lubrimat®
Thread cutting
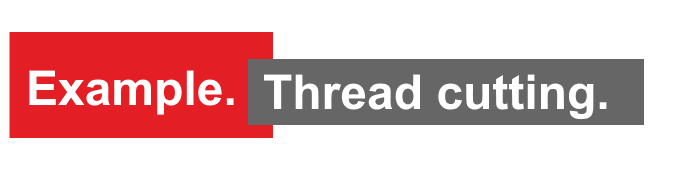

Thread cutting with Lubrimat®

Thread cutting with Lubrimat®

Thread cutting with Lubrimat®

Lubrimat® on a turning CNC lathe GILDEMEISTER

Tapping M4 x 9 in zinc die casting with Pulsomat®. Prior drilling of the cored blind hole. A single droplet of lubricant is fired onto the tool with a very high degree of accuracy, prior to its use. 20 litres of MQL lubricant is sufficient for an annual output of 1.2 million threads.

Thread cutting with in Aluminium (AlM6Si) with Pulsomat®

Thread cutting with Lubrimat®

Tapping M20 x 40 in 42CrMo4 with Deltamat® D40. A nozzle sprays the tool. Compared to previous manual lubrication, the average cutting values were increased, thereby reducing production times.

Thread cutting with two Pulsomat®

Thread cutting (brass) with two Pulsomat®
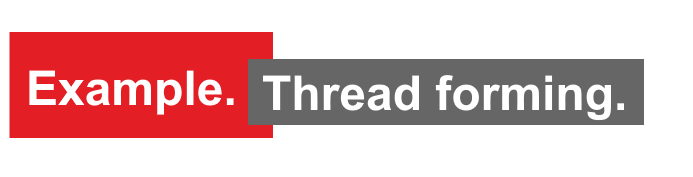
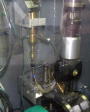
Thread forming with Pulsomat®
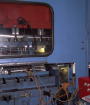
Thread forming with Lubrimat®
Turning
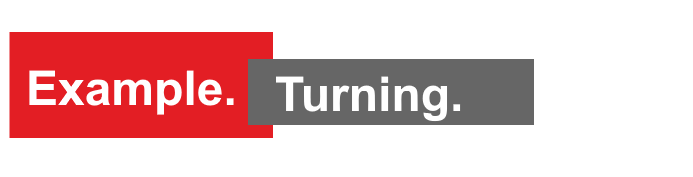

Turning of grooved rolls Ø1,500 mm made of forged steel with Lubrimat®. The diamond edges of the lathe tools were lubricated using one nozzle to prevent them becoming too hot and consequently coming loose.

Turning of aluminium screws with Lubrimat®.

The man on this lathe was suffering permanent skin irritations due to the coolant contact. Now, lubricating with Lubrimat®, the skin has recovered.

Turning of components for pump systems of high grade steel construction up to Ø1,200 mmwith Lubrimat®. 2 nozzles lubricate the tool. The heavy pollution of the area around the open machinery, associated with conventional flood cooling, was also largely eradicated.

CNC lathe TRAUB TND 360 with turret head and indexable insert holder. The nozzle of a Lubrimat® is integrated.

Turning with Lubrimat®
Grinding
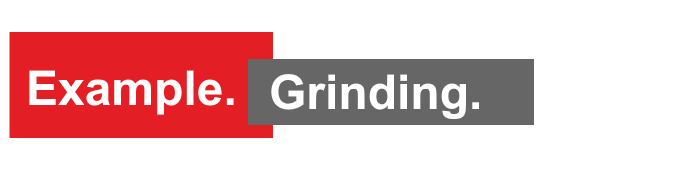

Grinding stainless steel knfes with Lubrimat®
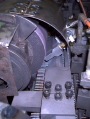
Grinding steel pins with Lubrimat®
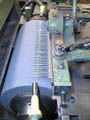
Grinding steel needles with Lubrimat®

Grinding of HSS drills with CBN grinding wheels, sprayed by Lubrimat® with 3 nozzles. Compared to flood cooling, the method used previously, the finished surface is now greatly improved and the work environment remains cleaner.
Broaching
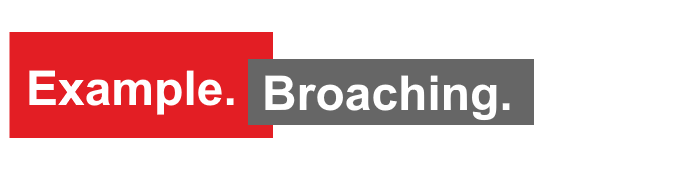
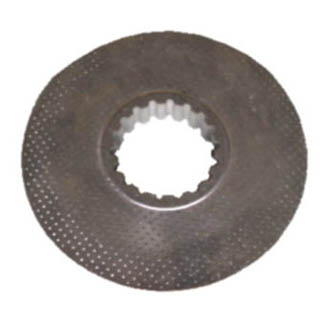
Broaching of coupling supports for lifts made of aluminium alloy with Lubrimat.

Broaching at the automotive industry with Lubrimat.
Milling /Engraving
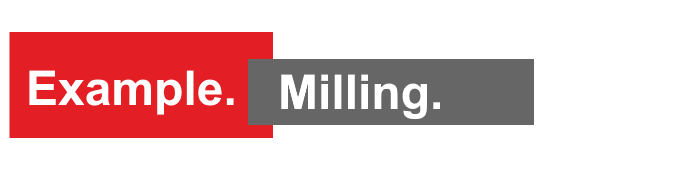

Milling and drilling with Lubrimat®.

Milling aluminium profiles with Spraymat®.
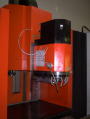
Milling of plastic parts on a machining centre with D Lubrimat®. Because emulsion would attack the plastic, until the introduction of MQL, dry processing had been used. However, this meant that the surface of the finished product was often unsatisfactory. Now the milling process is lubricated using one nozzle. This has improved surface quality, and has even made a gloss effect possible on some types of plastic.
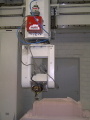
Lubrimat® enables a die maker to run the machine tool at nigth without workers.

Milling of several aluminium and steel profiles with Lubrimat®.

Milling with Lubrimat®.
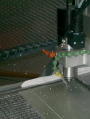
Milling of aluminium with Spraymat®.

Milling in hardened tool steel (60 HRC) with Lubrimat®. Mould making with a processing time of 3 hours per workpiece. In the case of dry processing, the edge life was not sufficient for one workpiece. 2 MQL nozzles lubricate the milling cutters and double the edge life. Thus, tool replacement during processing operations is no longer necessary.

Milling of ring T-nuts in surface plates (Ø up to 3,000 mm) of St52 constuction with Lubrimat®. Because of the size of the parts and the open construction, flood cooling is not possible. Two nozzles lubricate the milling cutters. There was a 100% increase in the edge life compared to dry processing.

Milling of a compressor rotor made of alloyed steel with a milling cutter Ø 250 mm with Lubrimat®. Compared to dry processing, the use of MQL resulted in increased edge life, improved finished surfaces and a reduction in the temperature of the workpiece.

Milling copper with Lubrimat®

HSC mould milling machine type MAGNUM with Lubrimat®

Lubrimat® lubricating the milling process of turbine elements on a hexapode machine tool

Milling aluminium with Lubrimat®

Milling with Lubrimat®

HSC milling with Steidle® Lubrimat®

Milling with Steidle® Lubrimat®

Groove milling with Steidle® Lubrimat®
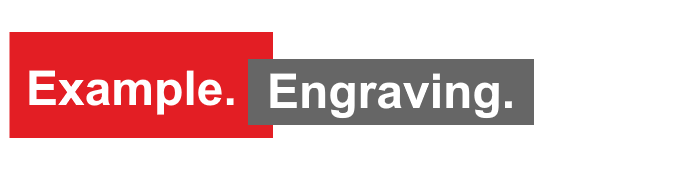

Engraving coated aluminium sheets with Lubrimat®. Because one nozzle lubricates the process, the workpiece remains so clean that it can be painted directly without the need for the components to be cleaned. Prior to the use of MQL, flood cooling was used and all the workpieces had to be washed.
